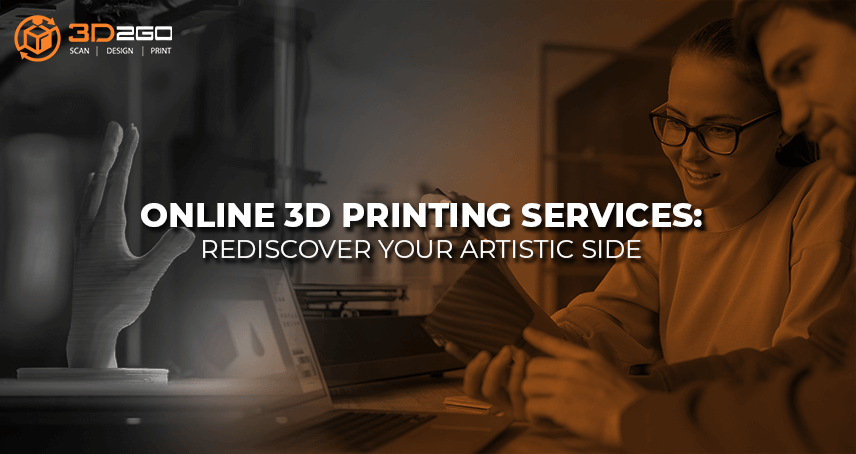
Online 3D Printing Services: Rediscover Your Artistic Side
June 4, 2022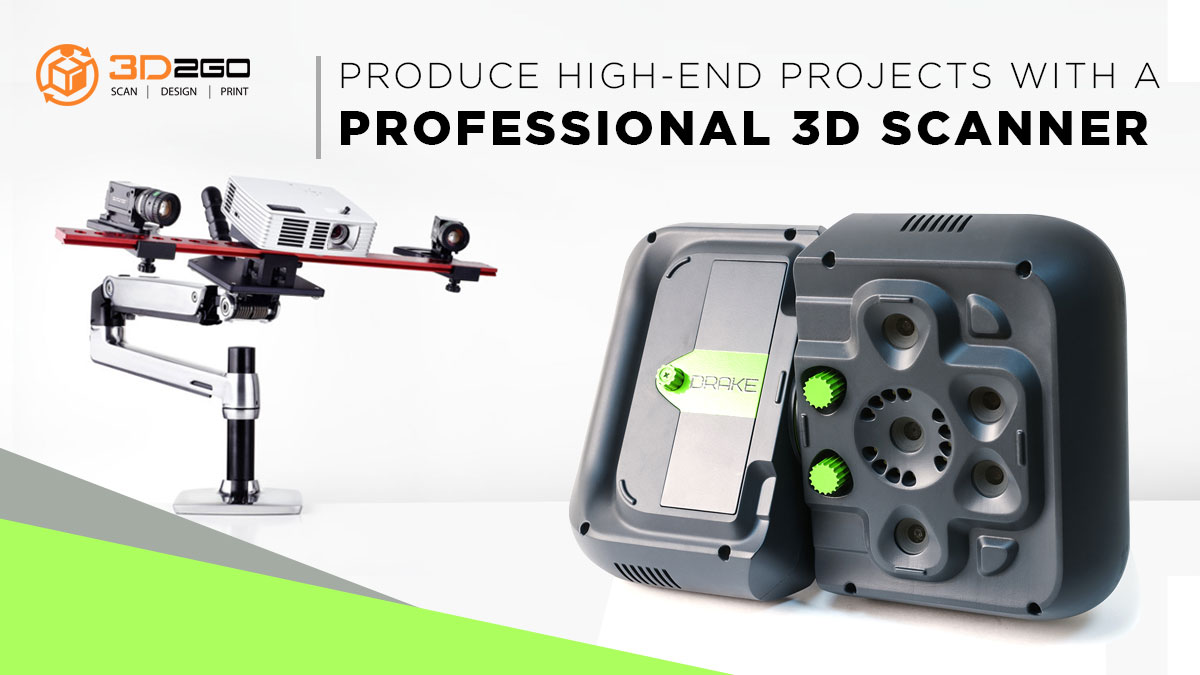
Professional 3D Scanners At Your Service
June 4, 2022Practical applications of 3D Printing in the automotive industry
Adoption of Additive Manufacturing (AM) is substantial in the last three years in various industries. Among them is 3D printing in the automotive industry.
While it started as an effective tool to increase rapid prototyping efforts, it has matured and brought innovative and consistent increase in research and development.
Leading automotive manufacturers such as Ford, General Motors, Volvo, Porsche, Volkswagen, and many more rely on this technology to develop more applications and further increase its adoption throughout the industry.
In addition to that, it helps accelerate product development cycles. As well as reduce resources like time and energy.
Real World Examples of 3D Technology in Cars
3D printing in automotive has been transforming production workflows, from R&D to supply chain and production.
Here are examples of 3D printing in automotive manufacturing.
1. Ducts and Brackets
Its application is for the Cadillac Blackwing V-Series and the first vehicles to use production 3D printing at a much bigger scale. It features two 3D printed nylon HVAC ducts created using Multijet Fusion, aluminum bracket made with powder bed fusion, and the shift knob’s stainless steel medallion made using binder jetting.
Adding to that, is Aston Martin Callum Vanquish 25 by R-Reforged’s brake ducts and switch holders. It features 3D printed brake ducts. This creation is possible through revision of the car’s front bumper, hidden parts and replacements since its components are no longer available.
2. Parking Brake Brackets
This is used for the Ford Mustang Shelby GT500 and it features plastic parking brake brackets created through Digital Light Processing (DLP) as a replacement for stamped metal parts.
This 3D printed component is much lighter than its predecessor. At the same time it allows design improvement, making it ambidextrous.
3. Gear Lever and Pedals
The 2021 Dakar Rally off-road racing vehicle has a customized gear lever and three brake pedals 3D printed in titanium. They use bed fusion technology to create better exhaust ball joints which previous designs are prone to breakage.
While this is a limited production, it opens the opportunity for other future cases in higher volume production.
4. Brake Rotors and Radar Antennae
An excellent example of this is Ceramic Disc Technologies’ 3D printed brake rotors from a ceramic-matrix composite for thermal control and strength.
Also Lunewave is using 3D printing to create antennae for their radar units.
5. Anti-theft Wheels Using Lug Nuts
There is a practical application in Europe wherein they 3D print custom locking wheel lug nuts for cars. These are more resistant to theft.
Ford is utilizing this innovation as well. Here they 3D print patterns for their locks that are much harder to copy. Customization for each customer is also possible as Ford uses sound waves from a simple sentence which creates an added layer of security.
Benefits of 3D Printing in the Automotive Industry
These are the general benefits of automotive applications in 3D printing:
- Parts prototyping
- Faster production of tooling, jigs, and fixtures
- Customization and personalization of parts
- Low volume or on-demand production of spare parts for classic models and discontinued cars
Design and concept of communication
3D printing outputs are often high detail, smooth and accurate. Thus an effective way to demonstrate designs and concepts of new vehicles. As CAD models are often not enough, 3D printing design prototypes are also effective for aerodynamic testing of new models.
Prototyping validation
Prototyping is also an important factor in the automotive industry. 3D printing in general allows rapid prototyping even in the pre-manufacturing stage. Thus is an effective tool to validate a prototype, its functionality and aesthetics.
3D printing automotive prototypes are also flexible enough to quickly print low detailed to high detailed parts. Both are suitable for performance validation and testing. It also allows ideas to turn into convincing proof of concepts.
Additionally, it increases iteration cycles and shortens the distance between idea and final product, thus strengthening overall product development workflows.
Pre-production sampling and tooling
3D printing is perfect to make molds and thermoforming tools. Its application also ranges in rapid manufacturing of grips, jigs and fixtures in low volume.
This allows automotive manufacturers to produce samples and tools at a much lower cost. It also minimizes future asset loss in production instead of investing in high-cost tooling.
Customized parts
A lot of automaker enterprises capitalize to tailor and customize parts for specific vehicles. This could be in the form of making custom parts lightweight and customized for specific owners or in this case, drivers.
This is also the perfect technology to create unique or enhanced components for improved performance of the vehicle.
Also it provides vital room to experiment with and to perfect custom designs. While in reduction of the potential expense and time-intensive manufacturing processes that comes with customization.
Fuels the rise of electric vehicles
To be environmentally-friendly is becoming the spotlight for a lot of industries, of course as well as in the automotive sector. Thus alternative ways to lessen carbon emission such as Electric Vehicles (EV) are gaining popularity with consumers.
The focus is on the effort to reduce the weight of the batteries that power EVs. as heavier components impact the efficiency and performance. Thus design engineers rethink how to recreate components which results in parts with unique geometries that allow weight reduction.
Solves the spare parts problem
Spare parts production has been a problem for the automotive industry. This is because demand is unpredictable and may result in financial instability. Also spares production in anticipation of later demand often requires spending on storage facilities.
3D printing is an advantageous technology to solve such problems. As it encourages low volume and on-demand production of spare parts. This results in a much cost effective approach while staying up to date with demand.
Also its CAD files are perfect to store as digital copies instead of inventories that withers away in warehouses. This provides the ability to produce only when needed.
3D2GO Provides End-to-End 3D Printing Services for the Automotive Sector
As the pioneer of 3D printing and its related services in the country, we have excellent services that continuously cater to the automotive industry.
3D2GO Philippines also offers 3D scanning, 3D designing and modelling, 3D rapid prototyping and 3D reverse engineering. We are the best 3D company when it comes to anything 3D-related.
Contact us today and let our services streamline any of your projects.