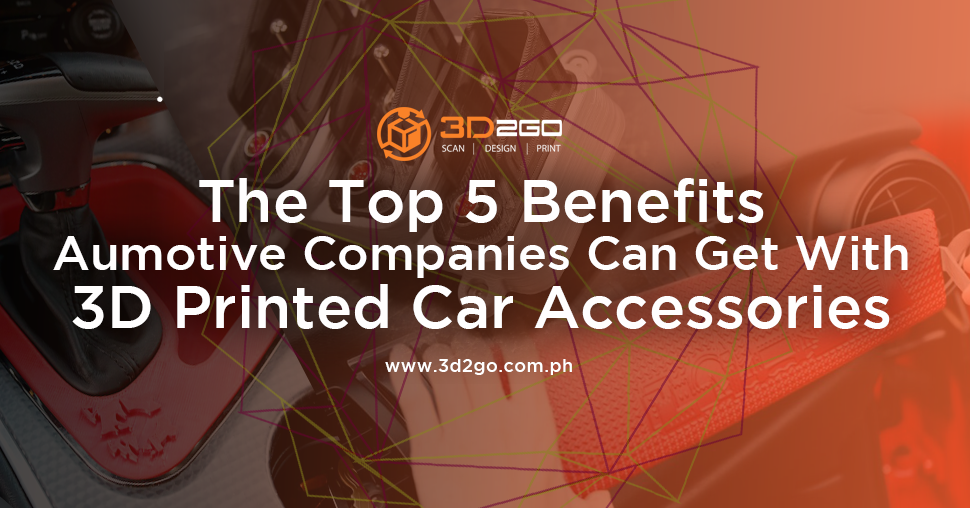
Advantages of 3D Printed Car Accessories
June 23, 2022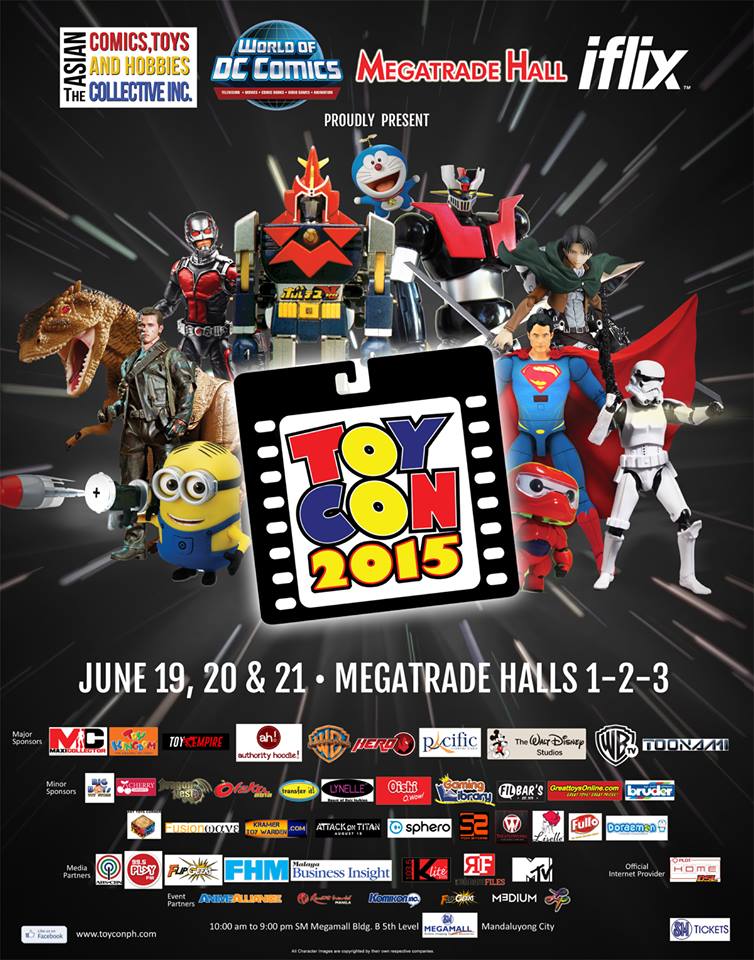
3D2GO Joins TOY CON Philippines 2015
June 24, 2022
How the Philippines can utilize 3D printing in the automotive industry
3D printing in the automotive industry is proving vital not only for design purposes but also in the assembly line.
This is not to say the Philippines’ automotive sector is yet to utilize 3D printing. In fact, automakers and assembly lines in the country from industry players to enthusiasts are using this technology.
3D printing is offering a lot of innovative ways for this sector in the country and with 3d printers coming up with more advanced features, it is no doubt it will become a staple in the industry in the years to come.
As this technology has been proven a cost-effective solution for the following purposes:
- Improve measurement
- Functional testing
- Vehicle customization
- Optimized design and rapid tooling
These factors are often critical for engineers, plant workers and designers for the automotive industry and thus making the field competitive.
The practical application of 3D printing for cars is to create automotive prototypes to validate their form and fit. The two popular methods for this are selective laser sintering and binder jetting.
This helps automotive manufacturers to rely on additive manufacturing to accelerate the production cycle and development which reduces time, energy, and money. In addition to that, it also improves the R&D, supply chain and the production.
Ways to Utilize 3D Printing Design and Development in the Philippine Automotive Sector
The Philippine automotive sector can utilize this technology and incorporate it for a better car manufacturing development cycle. Here’s how:
1. Reshapes the Prototyping Process
Historically, prototyping is the common application of 3D printing across manufacturing industries, automotive included. As this provides speed and optimal product output. That is why rapid prototyping became synonymous to 3D printing.
This led to revolutionizing of the product development process. Through rapid prototyping, it can help you fabricate a prototype or 3D scale models of a physical part or assembly. Which in turn can be convincing proof of concepts.
In addition to that, you can also create functional prototypes to show its mechanism. Thus moving beyond concepts and ideas. This strategy can help you win more clients and convince investors to fund your designs.
Aside from that, 3D printed prototypes can also guide you through the product’s validation stages. 3D printers have the capability to produce high-end prototypes within a matter of hours and at a much lower cost.
2. Create Custom and Complex Yet High Performance Spare Parts
3D printing has been proven ideal to produce custom parts at a much lower cost in comparison with traditional tooling methods. This advantage empowers manufacturers to explore new ideas to produce products and offerings to customers.
In addition to that, it also provides the necessary room to experiment and perfect custom designs without the hassle of additional expenses and time requirement. Furthermore, it pushes for quality and creativity in design and mechanism of the product and the overall assembly method.
3. Augments Tooling and Manufacturing Aids
Engineers and manufacturers use 3D printing to make the assembly process more simple and reliable. This results in reduced cycle times and workers safety conditions.
Additive manufacturing can cut the lead times in producing custom jigs and fixtures versus traditional machining services. As delayed times can lead to delayed production on the factory floor.
Also, this method enables better optimization for the end-use purposes. 3D printing materials allow manufacturers to replace metal components in many cases with 3D printed plastic parts. They can test the tools before they commit before additional expenses to incur.
4. Solution to the Spare Parts Problem
In the automotive industry, the spare parts demand is unpredictable which represents a challenge for this sector. Producing spare parts is often a source of debate as it impacts financial decisions in some cases. Spares production in anticipation of later demand also requires expenditure on storage.
3D designing and modeling can turn all these parts into a digital copy. In addition to that, desktop 3D printers can produce the spare part in-store, upon customer’s request or as-needed.
This accessibility encourages suppliers to open up new avenues for 3D printed components and spare parts. Unavailable parts for classic cars can be remade through reverse engineering via 3D scanner.
5. Improves General Parts Manufacture
The 3D printing process becomes more affordable in relation to the cost of hardware and materials involved. It also has the ability to produce consolidated parts which can help decrease weight and improve fuel efficiency.
Furthermore, 3D printing materials are starting to meet the mechanical standards of different vehicle’s components. This can significantly improve the financial aspects of the automotive manufacturing industry without sacrificing the quality and performance.
6. Avoid Supply Chain Disruptions
Additive manufacturing can help streamline the process of creating production parts on-site. This is practical should there be disruptions in the supply chain. Also it reduces the need for costly warehouse space.
This is possible through an optimized 3D CAD file for 3D printing which results in an end-use production part minus the time required for re-tooling.
Choose 3D2GO Philippines for your 3D Printing for Cars Requirements
As the pioneer of 3D printing Philippines, we strive to provide only the best services for various industries, namely the automotive sector.
Our services include 3D scanning, 3D designing and modeling, 3D reverse engineering, and 3D rapid prototyping.
3D2GO Philippines remains steadfast in its vision to provide the best 3D services and products for various Philippine sectors.
Let us help you utilize these various advantages for your business. Contact us today!