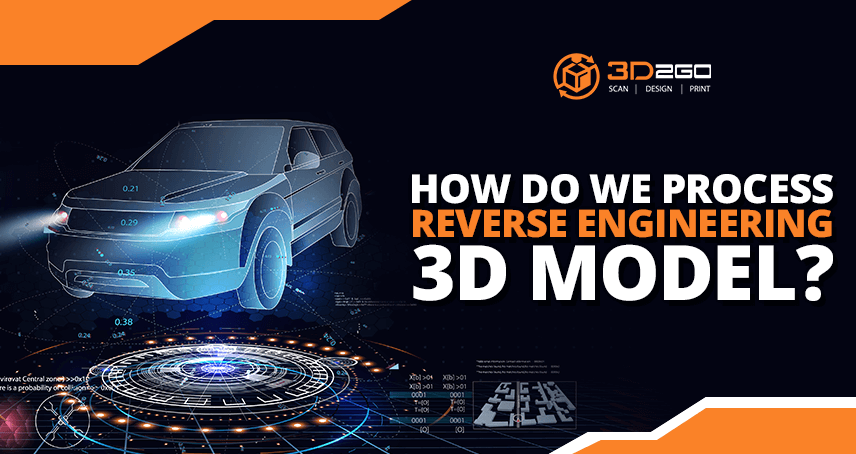
How Do We Process Reverse Engineering 3D Model?
July 15, 2022
3D Architectural Walkthrough Services For Game Developers
July 16, 2022
3D printing in medicine offers alternative approach in manufacturing NP swab tests
The COVID-19 pandemic posed a lot of problems, not only on health matters but on how pandemic cripples the medical supply chain. Good thing that 3D printing in medicine has helped to relieve such supply bottlenecks.
For instance, the sudden demand for personal protective equipment (PPE), ventilator splitter, face shields and the swab test kit is no longer attainable by traditional manufacturers.
This is where 3D printing has helped enough to ensure there is supply while traditional manufacturers keep up with the demand.
How 3D Technology For Medical Applications Help During the Pandemic
The breakthrough however, is the 3D printed nasopharyngeal (NP) swabs which have great demand due to extensive testing around the globe.
These NP swabs are made with a polyester handle and a top with tiny rayon or nylon fibers. This is inserted through the nose, deep into the nasal cavity where the sample is taken and broken off into a sealed vial to transfer into a testing lab.
These NP swabs are produced, assembled, sterilized and packaged using proprietary manufacturing methods and equipment. To which companies unprepared for the sudden demand plus the supply disruptions.
The Origin, a company acquired by Stratasys then produced clinically-tested and FDA-registered test swabs.
This was possible through collaboration with Henkel, Harvard’s Beth Israel Deaconess Medical Center (BIDMC) and other 3D printing leaders. The goal is to develop a one-piece, FDA-compliant, and sterile 3D printed NP test swab.
Another leading 3D printer that stepped up to meet this demand is Formlabs in collaboration with USF Health and Northwell Health. They developed and secured prototypes that are biocompatible and autoclavable resins.
How the project came into fruition:
Origin’s team validates the swab’s mechanical capabilities and manufacturability. While the Henkel as the material provider tested the swabs for biocompatibility and the validation of complete workflow
Process involved to ensure safety for human use:
The NP 3D models went through phase 3 human clinical trials wherein they determined that these 3D printed NP swabs are with high concordance and statistically indistinguishable from traditional swabs.
The Role of Custom 3D Printing For Medicine Supply Blockage
While traditional manufacturing methods eventually have kept up with the demand, the creation of a 3D printed NP swab is a prime example of a 3D printer’s ability to react to the medical supply chain disruptions.
This is possible because it can efficiently increase or decrease production to meet the demand. Thus not entirely dependent on bulk production which means lesser waste materials.
3D printing allows fast prototyping, accessibility and in-house fabrication of high demand PPEs, face shields, and NP swabs.
In addition to that, it enables people from different backgrounds such as medicine, engineering, and R&D worldwide to share and exchange design ideas and protocols to create diagnostic and hospital care devices.
3D printing technology is innovative itself but the pandemic supply demand further enables the introduction of 3D printing methods and fabrication to fight against the pandemic.
Current and Future Challenges of 3D Printing and 3D Models in Medicine
3D printing is the perfect technology to fill the gaps for supply chains in various industries, for this instance the medical field. However, current technology also provides critical shortcomings that makes this not suitable for everyday use. These are the following:
- 3D technology requires engineering skills and expertise. This is to design and model 3D CAD files.
- 3D models mostly require post-processing such as support removal, washing and post-curing. These methods require the necessary knowledge to perform successfully.
- 3D printers require consistent maintenance which includes cleaning, calibration and replacement of consumables and disposable accessories.
- Large scale production using the current 3D printing speed and setting requires a lot of money and production time which is still a challenging issue in a pandemic.
- Biocompatibility of materials is a top priority for 3D printed materials for medical-related purposes. 3D printing as an alternative manufacturing approach may mean decentralized fabrication. This could lead to unregulated use of tools which might raise safety concerns about wrong material selection.
Pros and Cons of 3D Printing in Medicine
While 3D printing helps in the surge of demand for medical supplies such as PPE, face shields, and NP swabs, there are still pros and cons of using this technology. These are the following:
Pros | Cons |
Personalized and patient-specific medical devices and implants3D printing has the capability to create medical devices according to the patient’s physiology. This is more effective than a mass-produced device. It’s a practical application like for knee surgery where it reduces pain levels. |
It is not eco-friendly3D printing uses plastic and energy. While there is less wasted materials in this method, the high energy it requires still has an undeniable impact on the environment. |
Timely manufacturing approach to on-demand devicesFor low volume production, 3D printing has the speed to create devices in response to patient demand. Its speed and flexibility help reduce waiting times for patients and lowers the chance of complications due to unavailable medical devices. |
Limited options of 3D printing materialThere is still a vast limitation on materials for 3D printing. Thus medical devices that require special or non-printable materials are still impossible to create. This is especially true in the Philippine context. Plastic is still the go-to material when it comes to 3D printing in the country. |
Rapid medical prototyping3D printing is still much cheaper and often faster than traditional manufacturing techniques. This means manufacturers and designers can design, print and test medical devices prototypes. For 3D models of medical prototypes, it is easier and quicker to modify within a span of a few days. |
Inconsistent quality of the 3D printed outputObjects that come out of 3D printers do not offer consistent results. This means there could be variations in dimensions and in texture where it needs to be smooth. Thus post-processing is still a necessity which may cost additional money and time to finish. |
3D2GO Philippines Provides 3D Printing and other Related Services for the Medical Sector
As the pioneer of 3D printing in the country, we stepped up during the pandemic when there was shortages in face shields for the medical sector in the country.
We continuously delivered excellent services such as 3D scanning, 3D designing and modelling, 3D reverse engineering, and 3D rapid prototyping for every sector amidst the pandemic.
3D2GO Philippines pledges to provide only the best services for every sector. Let us help you utilize these technologies for your advantage.