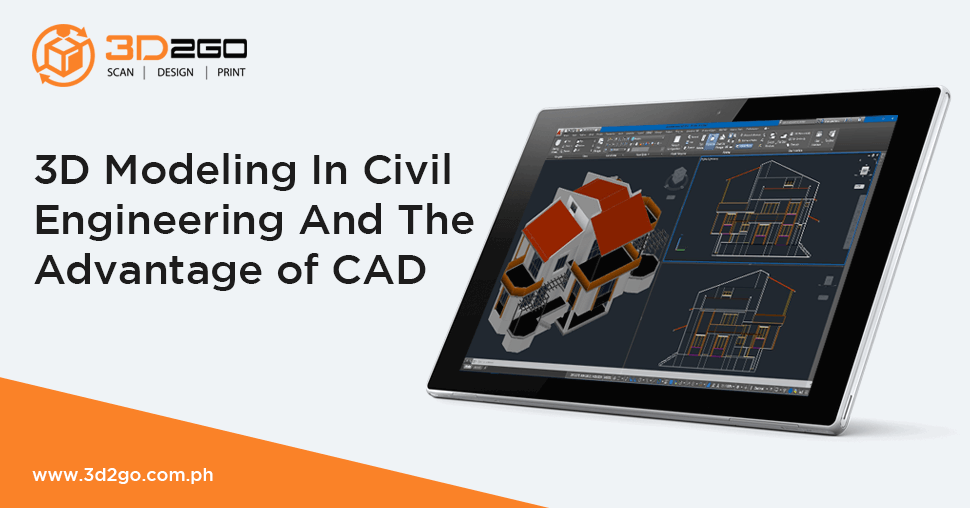
3D Modeling In Civil Engineering And The Advantage of CAD
July 12, 2022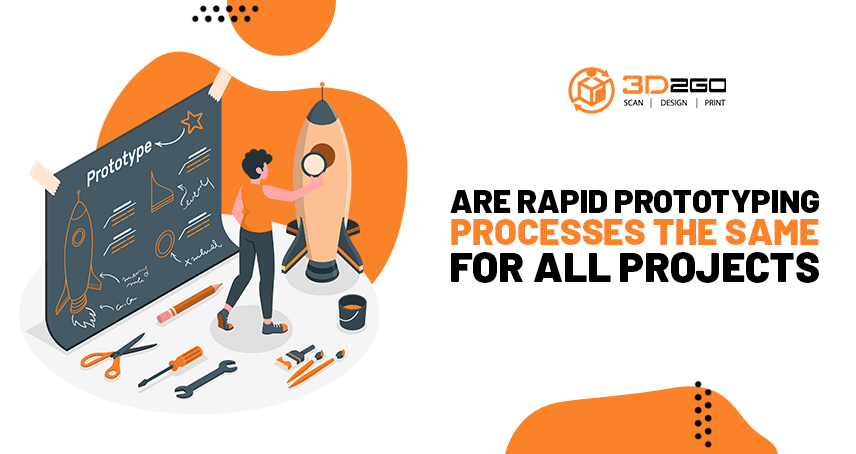
Are Rapid Prototyping Processes The Same For All Projects?
July 13, 2022At one look it is easy to see that 3D printing has absolutely no place in an industry as complex and unforgiving as aerospace. After all, this technology and industry involve aviation and space flight. You may think that it takes a considerable amount of time, money, and effort in launching a new consumer product; what more if it has something to do with the earth’s atmosphere and the space beyond?
Well, a whole lot. It turns out that the efficiency and effectiveness of 3D printing is already being felt in the aeronautics industry. For prototyping as well as tooling and producing parts and components, aerospace engineers turn to fused deposition modeling. That’s because this procedure works well with high-performance thermoplastics, which are plastic materials that become moldable beyond a certain temperature but solidifies when cooled.
It doesn’t come as a surprise that the National Aeronautics and Space Administration (NASA) is not new to 3D printing. In fact, their engineers bank on 3D printing when designing rovers and other specialized vehicles. Believe it or not, many of their parts are created digitally.
Apart from NASA, there are other institutions and companies that utilize 3D printing services. A great example is the aircraft company from the Czech Republic that saves a great deal of money on prototyping costs alone. Then there are the productions costs, so the company gets to keep more. In all, they are able to save up to 80%.
Now let’s take a closer look at how the aerospace industry benefits from this far-reaching technology.
Reduced Production Costs – Instead of using CNC-milled components which are obviously very expensive, aerospace engineers can utilize plastic parts that are manufactured in-house. Here, we are talking about a huge reduction in expenses. The money saved can be used for research and other important aspects of aerospace.
The great thing about it is that these 3D printing components not only cost less; they even perform better in a technical standpoint. They also weigh less and offer improved electrical insulation.
Easy Identification of Design Issues – If you are using only a computer-aided design (CAD) model, there are cases when it is not as effective in determining design issues as opposed to a 3D printed model. With the former, you can easily spot a problem that was overlooked in the initial stages.
This translates to better decision making and faster iterations. Problems are detected and corrected even before the component is produced. With 3D printing, companies not only save money but also time, which is way too precious in this industry.
Compatibility With Industry-Grade Materials – FDM machines partners well with production-grade thermoplastics such as the Ultem 9085. The Ultem 9085 is of course the best solution for manufacturing parts and components for aircraft because of its light weight. More importantly, it can withstand extremely intense heat more than any other material.