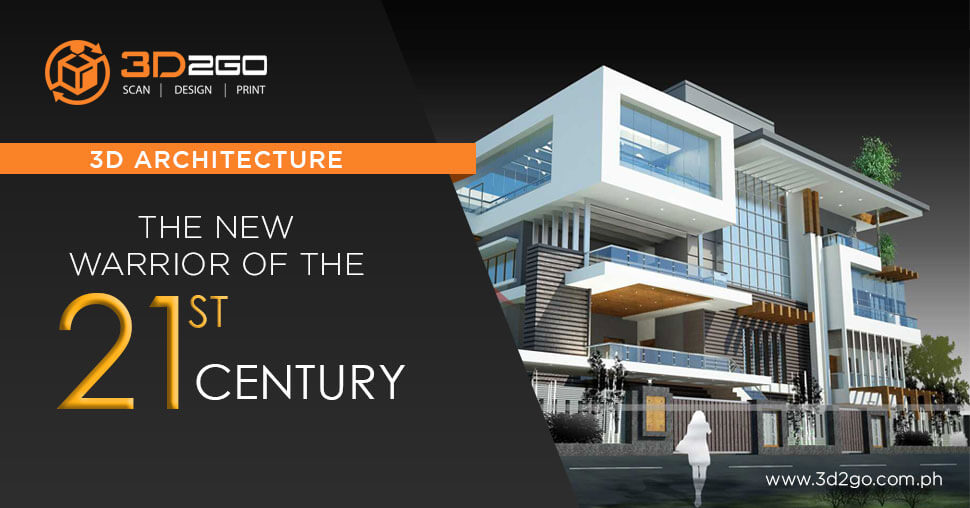
3D Architecture, The New Warrior of The 21st Century
June 13, 2022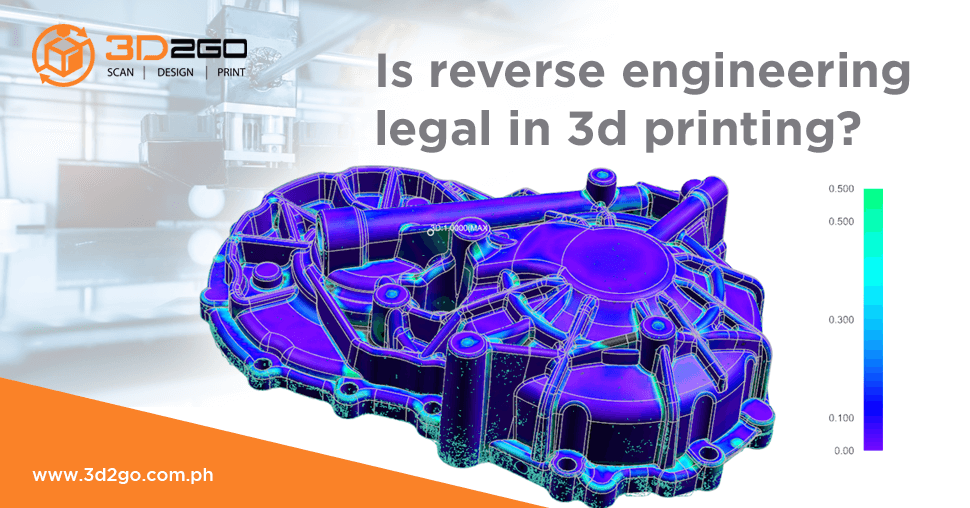
Is Reverse Engineering Legal In 3D Printing?
June 13, 20225 pillars of prototype manufacturing process
Ideally, your prototyping process should only take about a month or two at most, but the process may take longer depending on where you are in the design process.
1.) PROOF OF CONCEPT PROTOTYPE – will it work?
This is the first physical model created in the product roadmap. It is strictly concerned with function over form. Furthermore, it will likely bear little if any resemblance to the final product. This functionally representative prototype takes advantage of readily accessible materials to simulate its physical form while employing off-the-shelf technology to create its constituent components. This prototype is suitable for validating the viability of the product’s functionality. It is also tested in a variety of controlled settings.
2.) APPEARANCE PROTOTYPE – how will it look and feel?
The appearance prototype is visually representative while lacking actual functionality. It’s a static model without working features, wholly concerned with providing a sense of the look and feel. Engineers attempt to strike a balance between the use of viable materials and ones that aren’t prohibitively expensive. This prototype is also frequently used for sales and marketing.
3.) ENGINEERING PROTOTYPE
A direct successor to the proof of concept prototype. This prototype will usually resemble the final product in form but in a rougher or unfinished state. Designers may incorporate additional components to support the development process. As a result, these models may carry minor to significant differences in appearance. It’s also meant to be deployed for controlled customer and field trials in order to validate the design. The goal is to test the functionality of the product before a further investment into higher-grade materials is made.
4.) PRODUCTION PROTOTYPE
This is the last confirmation before designs are released for mass-production tooling. The key difference lies in the quality of materials used, as it is designed to be both fully functional and virtually indistinguishable in appearance from the final product. The final materials may be prohibitively expensive. Therefore, alternative materials are used to approximate the finished ones. While not yet totally ready for certification testing, this prototype serves as the final assessment.
5.) PILOT PROTOTYPE
The final prototype is really the start of mass production and is called the pilot. It’s constructed using mass-production manufacturing methods and could, in fact, be sold. Yet it’s still considered a prototype because of the need for product quality reviews and approvals.
3d prototyping service with 3D2GO
As you’ve seen, the product roadmap can be broken down into distinct phases. Each one contains its own set of milestones and goals. From the bare-bones proof of concept models to first off-the-line finished products, the prototyping process represents a progression from idea to reality. And for 3D2GO? Making everything a reality is our endgame.
fabrication of prototypes by engineers
Engineering teams synthesize this information to begin creating the product. Many times, something that works on paper proves to be very difficult to build. To help engineering teams assess the “buildability” of their project concept, they often create prototypes.
Want to start a pilot prototype of your own?
Get in touch with us by sending us files in .obj or .stil format in our email address management@my3d.com.ph. You can also reach us through our Facebook and Instagram pages today!