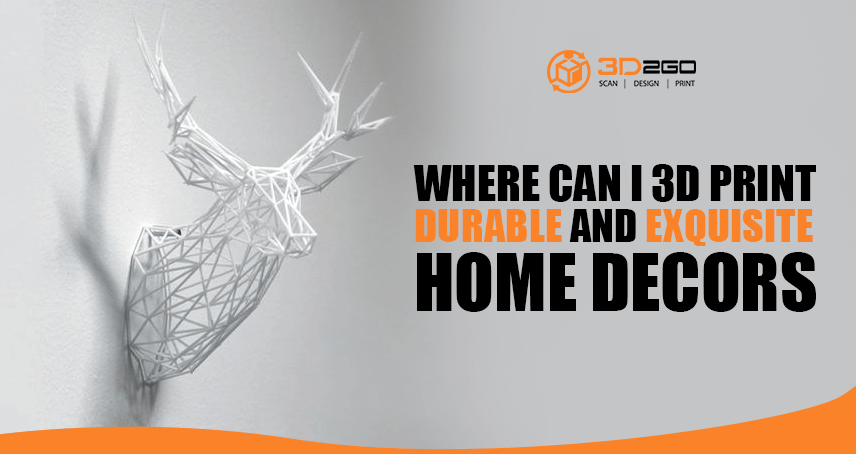
Where Can I 3D Print Durable and Exquisite Home Decors?
August 16, 2022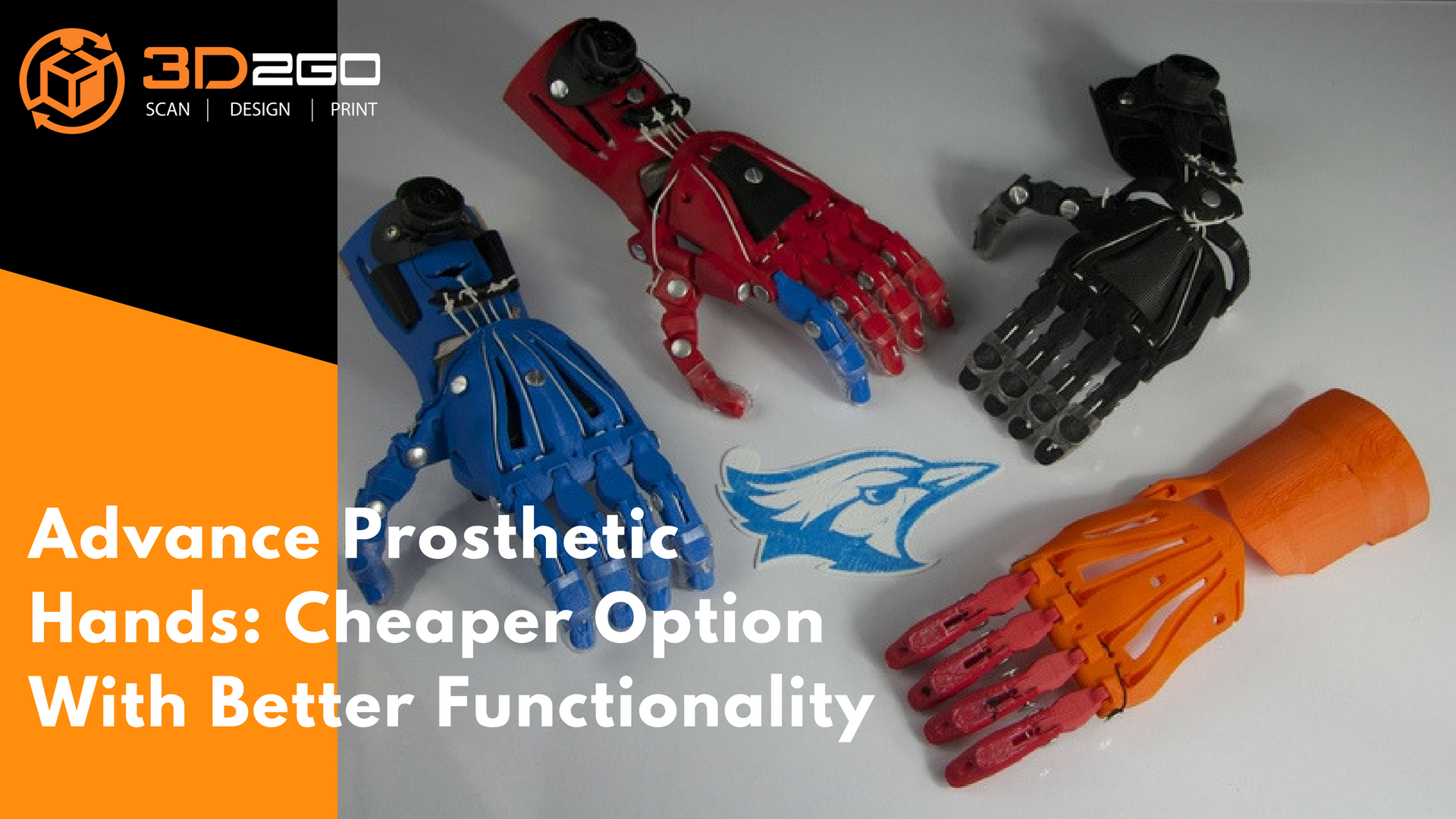
Cheaper But Better Advanced Prosthetic Hand
August 17, 2022
Traditionally, a designer has to consider three important parts in order to obtain a comfortable, elegant, and usable product: the form design, mechanical design, and construction design. Since “time to market”, function test, construction evaluation, and digital data have become such essential design factors of the design process, this project tried to develop an integrated design and manufacturing process which could be divided into the following steps: concept design, manual model, shape recognition, reverse engineering, CAD model, rapid prototyping, rapid tooling, and final product.
Also at some point, most manufacturers will need to replicate a part for which there is no original CAD file. Perhaps it’s a tool nearing the end of its life, a legacy part that was designed in the pre-CAD days, or a component that was modified after the CAD model was created. For this, you may wish to consider prototyping and reverse engineering the part.
What is Reverse Engineering?
The process of using an existing manufactured part to create a 3D model is often referred to as reverse engineering or reverse modeling. By utilizing reverse engineering, new designs can incorporate and improve upon engineering optimization already inherent to the manufactured part.
Who can profit from 3D modeling?
The quick answer is anyone in manufacturing, engineering, design, development, surveying or testing. 3D modeling and prototyping can be applied at any point in a typical manufacturing cycle, saving time, money and material. It results in higher quality, better fitting parts that are less costly to manufacture. The cost of a typical manufacturing design cycle is reduced by 75% by utilizing 3D modeling and prototyping.
3D modeling and prototyping can also be applied at the idea concept phase by digitizing objects, then using them as renderings in concept illustrations. Oftentimes, designers need to design around or fit their design to existing objects. These mating parts can also be scanned and incorporated into the design, resulting in parts that fit better on a consistent basis.
What are the benefits?
The benefits of prototyping and reverse engineering are significant to the way we manufacture and produce objects. Not only is the method extremely quick, it allows us to analyze and find flaws in the design before production begins thus saving companies a lot of money. The models can be functional for testing and there is less time and money committed to the overall patent and production process.
We can assess the quality of the aesthetics and manufacturability of the object as well as how useful it will be therefore determining what the next step should be in creating the product i.e. what machines will be needed to build a fully working model.
It also allows us to build extremely complex objects more easily and in a more innovative manner. As the design is built up through layering, this eradicates any issues that usually arise with other methods such as plastic injection moulding or hand-crafting.
Rapid prototyping has taught us that it is very much the next step in manufacturing. It paves the way for exciting new products using the simple click of a button. Of course there is the possibility that it may eradicate traditional manufacturing if it ever reaches the scale of being used for mass production yet it still gives us the power to recreate something into an almost perfect clone.