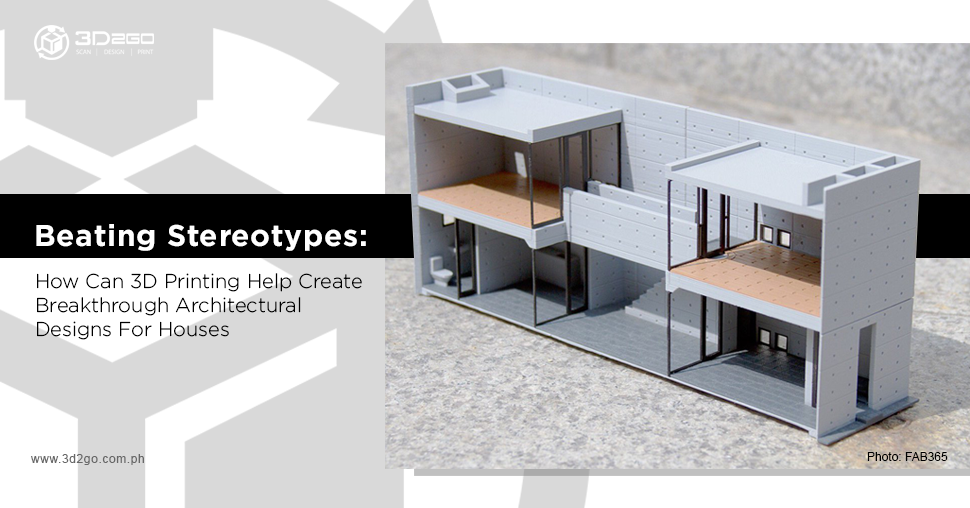
3D Printing Helps Breakthrough The Stereotypical Architectural Designs For Houses
June 29, 2022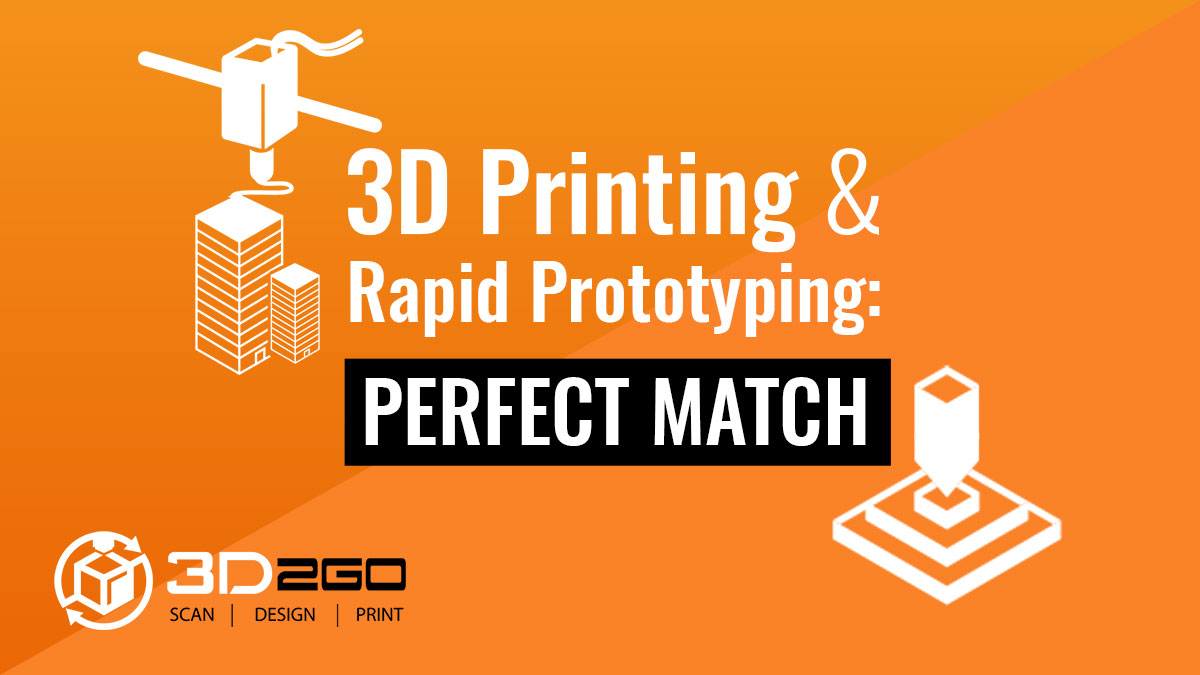
3D Printing and Rapid Prototyping: Perfect Match
June 30, 2022Advancement Of 3D Printing in the Automotive Industry
3D printing is not only just for DIYers and hobbyists. In the past decades, it has changed and evolved as a service and product.
The commercial benefits of 3D printing have already expanded to the automotive industry because of technological advances made. With 3D printing, manufacturers gain the ability to construct commercial and personal vehicles. Thus, cars are made more affordable and available than ever before.
How has 3D printing aided top car manufacturers?
3D technology has been an effective solution for prototypes, one-offs, and small volume production of parts. But can it find its way around high-volume production demands like 3D printing for cars?
3D2GO believes that 3D printing can indeed be made possible for high-volume productions. This is because manufacturers are choosing 3D technology for its design freedoms, lightweight possibilities, material options, and more.
It’s interesting to see how far 3D technology in cars has come, having big-named clients in the automotive industry. Provided below are 5 companies that have integrated 3D printing in their workflow.
BMW
The company has been pretty inventive with additive manufacturing (AM). With the technology, they have enhanced most of their plastic and metal components.
BMW has been using 3D printing to be able to produce parts that no other car manufacturer has done. One unique part they’ve done is the i8 Roadster’s top bracket.
Using a traditional casting process to create the top cover would be impossible. With 3D printing and AM, design possibilities can go beyond your limitations. This further makes the 3D printed car part more durable and weighs less than the previous successors.
Ford
Ford has been a leader in using AM applications across their production. They have cut costs and time for tooling. Moreso, they found quicker ways to make their own parts on the facility compared to waiting for suppliers.
Additionally, Ford’s subsidiaries showed off the Shelby GT500 from their AM process. They 3D printed designs for the GT500 in just a matter of days. As a result, it sped up the improvement and testing stages hugely. Because of this fastened process, they were also able to immediately make the needed changes for Shelby GT500, bringing in new physical designs at breakneck speeds.
The Ford Performance division has dealt with 3D printed high-performance components. This made them the manufacturer of the largest metal automotive part for a working vehicle in automotive history.
Volvo
Like the other companies on this list, Volvo has been using 3D printing for tooling and supply chain management. They mostly used 3D printing for plastic parts. Additionally, they are looking towards the implementation of metal materials in the near future.
The use of AM since 2018 has increased the speed of prototyping. Volvo engineers designed new water pump housings for their A25G and A30G vehicles. Simulations were run to further understand the design of internal flow passages.
In 2019, the company stepped up with its AM processes. Aside from the use of SLS, they have also experimented with other AM methods. As a result, their New River Valley (NRV) plant was able to produce over 500 manufacturing tools and fixtures.
3D printing has also made its mark on their construction equipment. Volvo applied 3D printing in re-tooling their articulated haul trucks, thus cutting down prototyping costs.
General Motors (GM)
GM was saving $300,000 a year when 2018 came for their tooling. They have also made advancements with the use of alternative fuel sources.
Although their 3D printing is mostly for prototyping purposes, GM further plans to expand and mass produce parts at scale.
GM’s Warren Tech Center produces 30,000 prototype parts. These consist of materials combining plastics, metals, and powders. Aside from prototyping, they are looking to have end-use parts.
Porsche
The company has been using 3D printing for a number of purposes. But because of stringent quality standards, 3D printing has mostly been limited to manufacture specific spare parts. Moreso, they only work with a lower number of units as they are leaning more on being a classic and luxury brand.
The development of Porsche 959, the company uses laser melting. They make use of powdered tool steel. This results in having a part that is more efficient than it would have been with other alternative methods.
Partner with the best 3D printing service in town!
3D printing for internal parts has opened the door to new solutions and design strategies.
With 3D2GO, we can enrich the car’s design process and the final outcome, while reducing the time-to-market and overall labor costs.
Are you interested to find out how 3D2GO can help automotive industries in general?
Get in touch with us in our email address management@my3d.com.ph. You can also reach us through our Facebook and Instagram pages today!