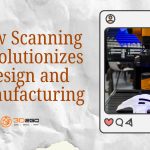
How Scanning Revolutionizes Design and Manufacturing
November 4, 2024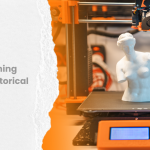
How 3D Scanning Preserves Historical Artifacts
February 21, 2025Traditional prosthetic limbs were often mass-produced, leading to a one-size-fits-all approach. This method frequently resulted in discomfort and limited mobility for users. The advent of 3D modeling has revolutionized this field, allowing for the creation of personalized prosthetics that match the unique anatomy of each patient.
In the past, prosthetic limbs were manually crafted, a process that was time-consuming and lacked precision. Today, with Computer-Aided Design (CAD) for prosthetics, designers can create detailed digital models that accurately reflect a patient’s limb structure. This shift not only speeds up production but also enhances the quality and fit of the prosthetics.
Integrating 3D Modeling into Prosthetic Development
The use of 3D modeling in prosthetics involves several key steps:
1. Digital Imaging and Scanning
Advanced scanning technologies capture the exact shape of a patient’s residual limb, which is used to create a precise 3D model.
2. Computer-Aided Design (CAD)
Specialized CAD software allows designers to develop detailed prosthetic models. These designs can be tailored to meet the unique needs of each patient.
3. Material Selection
Choosing the right materials is crucial for prosthetic function and comfort. 3D modeling helps in testing different materials digitally before production.
4. 3D Printing and Fabrication
Once the design is finalized, 3D printing technology brings the prosthetic to life. This method ensures a high level of accuracy and customization.
How 3D Modeling Transforms Prosthetic Limb Design
Prosthetic limb design has evolved significantly. Gone are the days of one-size-fits-all solutions. 3D modeling allows for precision and creativity in designing prosthetics.
1. Precision in Design
3D modeling uses computer-aided design (CAD) to create detailed prosthetic models. Every curve, joint, and angle is carefully planned. This ensures a perfect fit and better functionality for the user.
2. Faster Prototyping
Traditional methods can take weeks or months. With 3D modeling, designs can be tested and adjusted quickly. This speeds up the entire process, from concept to final product.
3. Customization for Unique Needs
No two patients are the same. 3D modeling allows for personalized prosthetics tailored to individual body shapes and needs. This improves comfort and usability.
4. Integration with Biomechanical Modeling
3D modeling works hand-in-hand with biomechanical modeling. This ensures prosthetics move naturally and reduce strain on the body.
Personalized Prosthetics: A New Era of Care
Personalization is the future of medical prosthetics. 3D modeling makes it possible to create prosthetics that feel like a natural body part.
1. Tailored to Body Measurements
Using 3D scans, prosthetics are designed to match the patient’s exact measurements. This ensures a perfect fit and better comfort.
2. Aesthetic Customization
Prosthetics can now look more natural or even reflect the user’s personality. This boosts confidence and mental well-being.
3. Improved Prosthetic Fitting Process
The fitting process is smoother with 3D modeling. Adjustments can be made digitally before the prosthetic is printed.
4. Enhancing Mobility and Independence
Personalized prosthetics improve mobility. They allow users to perform daily tasks with ease and regain their independence.
The Advantages of 3D Modeling in Prosthetics
-
Personalized Fit and Comfort
3D modeling provides a level of customization that wasn’t possible with traditional methods. Each prosthetic can be tailored to fit the specific measurements and anatomy of the individual, significantly enhancing comfort and functionality.
-
Reduced Production Time
3D printing and digital design streamline the entire process. From digital modeling to rapid prototyping, the time needed to create a prosthetic is drastically reduced compared to traditional methods.
-
Lower Costs for Patients
3D modeling can lower production costs by allowing users to quickly prototype and produce prosthetics. This can make high-quality prosthetics more affordable and accessible for a broader range of patients.
3D2GO Transforming Prosthetics with 3D
We offer end-to-end 3D services to improve prosthetic development, including:
- 3D Scanning. We use state-of-the-art scanning technology to capture exact limb measurements, ensuring a prosthetic that fits perfectly and enhances comfort.
- 3D Printing. Lightweight and Durable Prosthetics. Our 3D printing services create lightweight, durable prosthetic components that offer flexibility, comfort, and functionality.
- 3D Modeling & Rendering. We create detailed 3D models of prosthetics, ensuring both aesthetic and functional requirements are met, providing lifelike and practical solutions.
- Rapid Prototyping. Our rapid prototyping service allows for quick testing of prosthetic designs, ensuring each one performs well before moving on to full-scale production.
With cutting-edge technology, we help medical professionals and prosthetic specialists deliver personalized, high-quality solutions. Let us bring your vision to life—contact us today!